

#Arduino servo how to
Examples Servo SweepĪt this part, we will show how to use the Osoyoo Uno to sweeps the shaft of a RC servo motor back and forth across 180 degrees. Be sure to connect the grounds of the Arduin and external power supply together. Note that servos draw considerable power, so if you need to drive more than one or two, you’ll probably need to power them from a separate supply (i.e. The signal pin is typically yellow, orange or white and should be connected to a digital pin on the board. The ground wire is typically black or brown and should be connected to a ground pin on the board. The power wire is typically red, and should be connected to the 5V pin on the board. Servo motors have three wires: power, ground, and signal. On the Mega, up to 12 servos can be used without interfering with PWM functionality use of 12 to 23 motors will disable PWM on pins 11 and 12. On boards other than the Mega, use of the library disables analogWrite() (PWM) functionality on pins 9 and 10, whether or not there is a Servo on those pins.

The Servo library supports up to 12 motors on most boards and 48 on the Arduin Mega. Continuous rotation servos allow the rotation of the shaft to be set to various speeds. Standard servos allow the shaft to be positioned at various angles, usually between 0 and 180 degrees. Servos have integrated gears and a shaft that can be precisely controlled. This library allows an board to control RC (hobby) servo motors.
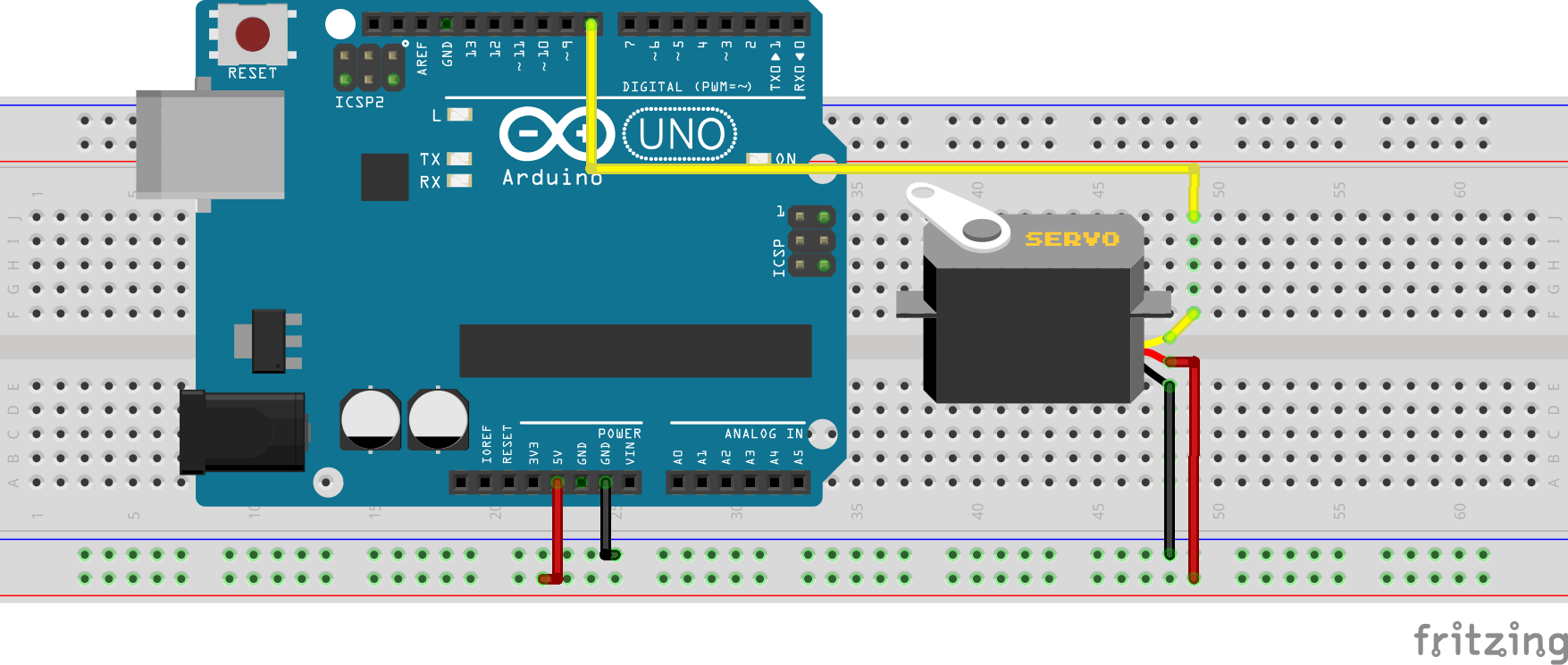
If this happens, then you can usually cure it by adding a high value capacitor (470uF or greater) between GND and 5V on the breadboard. This is because the servo draws quite a lot of power, especially as the motor is starting up, and this sudden high demand can be enough to drop the voltage on the board, so that it resets itself. Our servo may behave erratically, and you may find that this only happens when the Arduin is plugged into certain USB ports. The graphic makes it a little easier to understand. In between, it represents the value from 0–180. At 1 millisecond it represents 0 degrees and at 2 milliseconds it represents 180 degrees. At the beginning of each cycle, the signal is HIGH for a time between 1 and 2 milliseconds. Each cycle in the signal lasts for 20 milliseconds and for most of the time, the value is LOW. But what kind of signal do they receive on the input pin?
#Arduino servo driver
Internally, they have a motor driver and a feedback circuit that makes sure that the servo arm reaches the desired position. Using just one input pin, they receive the position from the Arduin and they go there. This control lead is connected to digital pin 9. The other lead is the control lead and this is usually orange or yellow. The color of the leads varies between servo motors, but the red lead is always 5V and GND will either be black or brown. Servo consists of shell, circuit board, non-core motor, gear and location detection.The servo motor has three leads. Osoyoo Basic Board (Fully compatible with Arduino UNO rev.3) x 1.In this lesson, you will learn how to control a servo motor using an Arduin.įirstly, you will get the servo to sweep back and forth automatically and then you will add a pot to control the position of the servo. With time, they found their uses in robotics, automation, and of course, the Arduin world. Servo motors were first used in the Remote Control (RC) world, usually to control the steering of RC cars or the flaps on a RC plane.

Using the Arduin, we can tell a servo to go to a specified position and it will go there. Usually, they have a servo arm that can turn 180 degrees. Servo motors are great devices that can turn to a specified position. Note: ALL OSOYOO Products for Arduino are Third Party Board which is fully compatitable with Arduino Content
